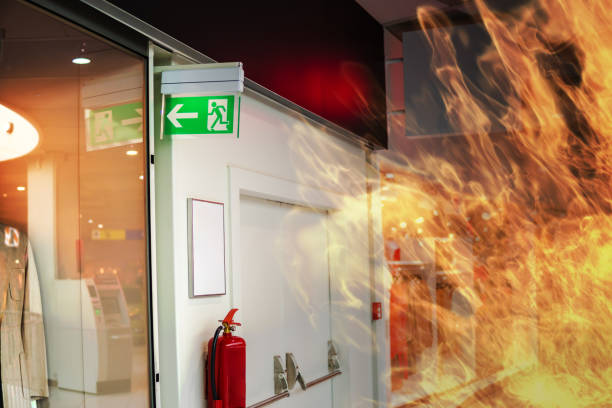
We are a leading manufacturer of quality internal and external lighting products for commercial, industrial and retail applications.
View all productsAt Ansell Lighting we design and manufacture an extensive range of luminaires for a diverse number of sectors and applications. Whatever the shape, purpose or style of your space, we have a lighting solution.
View all sectors & applicationsWe are a leading manufacturer of quality internal and external lighting products for commercial, industrial and retail applications.
Welcome to Ansell lightingWe are here to answer any questions you may have, help you find a stockist or speak to a local member of our team.
OCTO delivers the complete smart lighting package to transform the efficiency and ambience of commercial and residential spaces.
Find information regarding our product warranty, product data downloads and FAQs regarding lighting and technical terms. Here you will find support with training CPDs as well as useful lighting design and LED strip calculators.
In testing thermoplastic material for use as lighting diffusers installed into ceilings within buildings, BS 2782-0:2011 gives a general introduction to the methods of test for plastics. Within Annex A of the standard, is given the list of the individual methods published separately and degree of equivalence to the international Standards, whereas within Annex B, is described an obsolescent method (508A), as formerly detailed in an earlier standard, and which is still referred to by the Building Regulations.
Testing to Method 508A, was originally defined in BS 2782-5:1970 and was subsequently withdrawn by BSI in 1992 in classifying tested materials as being either TP(a) or TP(b), where a laboratory method is used for the testing process, where within the BS 2782-0:2004, Method 508A gives details of rate of burning.
Within the latest standard, BS 2782-0:2011 – Method 508A is detailed in Annex B, and clearly states that, “The method has been declared obsolescent but is made available here because it is referred to in the Approved Document B Building Regulations”.
The process of ‘Method 508A’ dates from when light sources were generally old technology, such as linear fluorescent and the installed optics were a single piece prismatic controller or opal diffuser.
In respect of the test specimen, and regardless of the thickness of the material used for the construction of the actual diffuser, a small piece of the material being used as the diffuser is required for the test process, of which the required dimensions are to be 150mm x 13mm x 1.5mm. Prior to the test process, two lines shall be drawn across the specimen, the first to beat 25 mm from the test point and the second to be at 125 mm from the same end.
The specimen sample is to be tested within a draught-free atmosphere and is to be clamped in a rigid support at one end so that its longitudinal axis is in the horizontal plane & its transverse axis is at 45° to the horizontal, being installed so that both lines on the specimen are clearly visible. A piece of clean wire gauze, of seven meshes per linear centimetre, and at a size of 130 mm square shall be clamped in a horizontal position 6 mm below the specimen with 6 mm of the unsupported end of the specimen projecting beyond the edge of the gauze.
The material is to be subjected to a naked flame for 10 seconds and the time taken for the sample to burn between two marks positioned 25mm and 125mm from the end of the sample is measured, as shown in BS 2782-0:2011. The results of the test will provide the classification of TP rating.
For the purposes of the relevant requirements, thermoplastic materials should be classified as being TP(a) rigid, TP(a) flexible or TP(b), where for,
TP(a) rigid – that for any other rigid thermoplastic product, where a specimen sample of which, at the thickness of the product as placed on the market, when tested to BS 2782-0 Method 508A, performs so that both, the test flame extinguishes before the first mark at 25mm, and the duration of flaming or afterglow does not exceed 5 seconds following removal of the burner.
TP(b) – that for other products which, when a specimen sample of the material of thickness between 1.5 and 3mm is tested in accordance with BS 2782-0 Method 508A, where classification indicates that the flame continued to spread along the material having a maximum rate of burning of 50mm/minute.
Where the material being tested does not satisfy either of the conditions described above, then the diffuser is deemed as being unclassified.
It is known that the properties of certain diffuser material can vary with the direction of the sample under test, either longitudinal or transverse and in practice to achieve compliance, it is usual to cut two groups of test pieces, one longitudinal to the main axis and transverse to the main axis, where for the testing of each material, this is carried out using both samples, giving a TP rating based upon the results of the two tests. For the lighting diffuser to gain either a TP(a) or TP(b) rating, both pieces of material are to achieve the appropriate classification.
The requirements of the Building Regulations are to resist the spread of flame, and once a flame is established, limit the growth of the fire. Testing is normally only carried out with the bottom material of the diffuser, which will give a good indication of resistance to ignition. Once the flame becomes more established it will no longer give a reliable indication on how the flame will grow and then spread onto all of the materials being used in the construction of the diffuser. Modern LED luminaires tend to use diffusers constructed of a composite of materials, termed as being of a ‘sandwich’ construction, and therefore the testing procedure should be based upon testing of the diffuser with a complete construction of materials as used within the recessed luminaire in order to achieve the appropriate result.